I also have a 40 minute streaming video on lamination techniques
https://vimeo.com/ondemand/laminatingcoloredclay
Lamination is the process of creating multiple layers of clay with these results -
- your finished Artwork has more strength
- your Artwork dries faster with less cracking issues
- your firing results are better … again, with less cracks
- your colored clay last longer
The #1 thing to always keep in mind is HUMIDITY
I cannot say this often enough.
Your pieces have to stay at the same humidity level
Letting your pieces get out of sync with each other will result in cracking.
This is why I always build a holding area for my work in progress.
I put down a piece of plastic, lie a damp towel on it and cover with another piece of plastic. Low tech … inexpensive … and it works to keep the humidity even on anything stored there. Whenever you are not actively working on your clay it should be resting there.
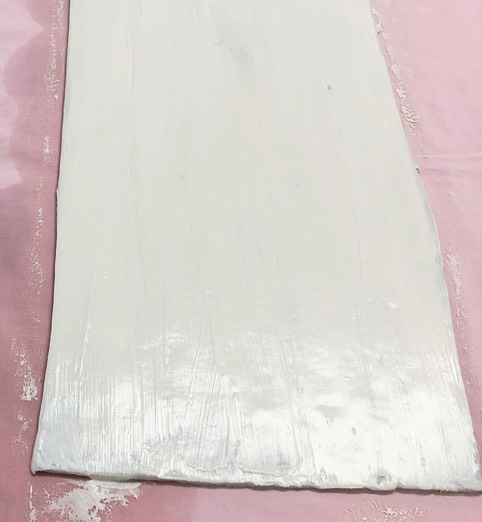
You can laminate your colored clay on to one side or both sides, so prepare your white clay by rolling it out to a bit less height than you want in the end. This white sheet can be as thin or thick as you want. If you have watched your humidity it will bond with your colored clay.
#1 - Joining by hand
The sheets above are resting after being rolled out to size. The colored sheet is made from pieces of canes and the other is a simple slab of matching white clay.
Let them rest on a damp towel under plastic for at least an hour or two. It is that simple. This gives them both time to shrink back a bit at their own pace and to reach a matching humidity level. You will have to learn to judge how long to leave them by touch and experience.
If one sheet is much dryer or wetter then wait until they are both the same. They do not have to be the same thickness, but wait until they match in humidity.
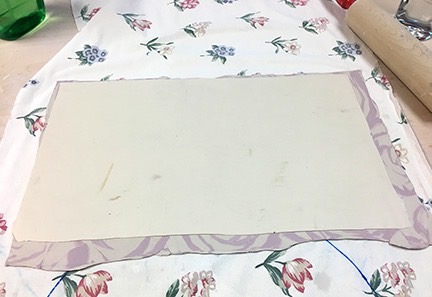
When you think they are ready, gently place one piece on the other without stretching either piece … you might need a very light spritz of water but not too much. Gently roll over the piece to make sure you don’t have any air bubbles. Use a sharp point to burst any bubbles that might occur.
After this I generally set the joined pieces aside for a few minutes … once again under plastic on a damp towel.
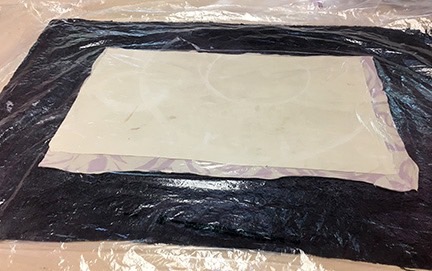
You might think this is 'over kill' on the babying and waiting, but it is not. You have put in so much work on this piece to get it to this point that waiting a bit for the clay to rest and equalize is going to prevent cracking.
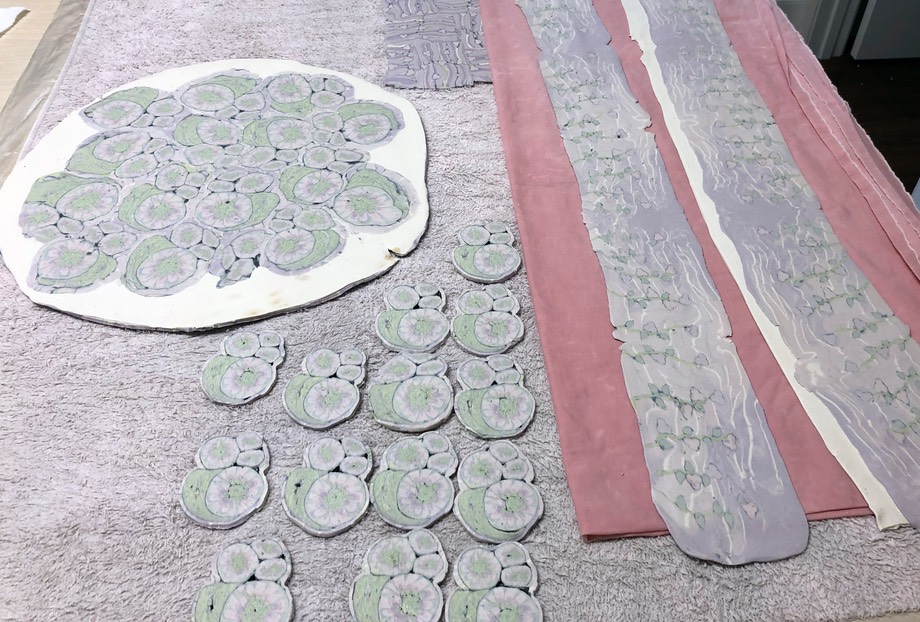
In this image you can see a thin sheet of color on a thicker sheet of white on the left.
On the right you see a strip of clay where I have rolled on the color and right beside it a matching sheet of color to be rolled on to the opposite side
In the middle are the sprigs of clay used to create the circle above them.
This image shows the moment before I start to gently roll the colored strip on to the white side of the clay strip.
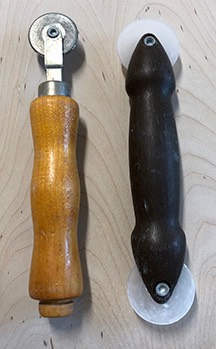
It already has the same pattern on the other side.
This tool is called a spliner and can be purchased in hardware stores. It is used in screen repair to wrap the screen.
It works wonderfully to wrap the clay, hiding the white layer in the middle.
Roll the spliner along the edge with a sheet of plastic over the clay.
This is the smooth edge you will get.
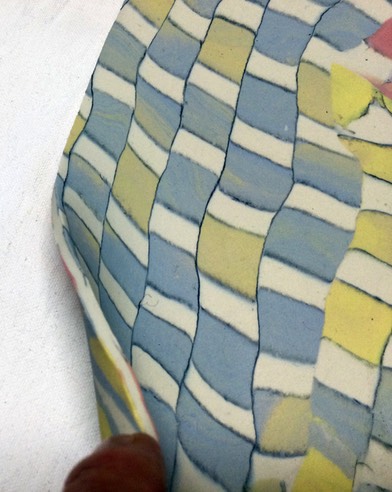
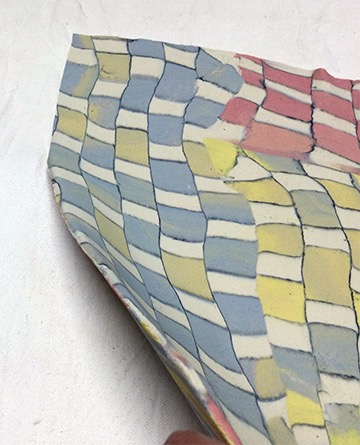
These two images clearly show the wonderful effect of the spliner.
This process uses sprigs from several canes to create a design then laminating it to a piece of white clay.
I am slicing the canes, creating a pattern and carefully patting them down.
Then I gently roll them together... make sure to only press DOWN, no stretching.
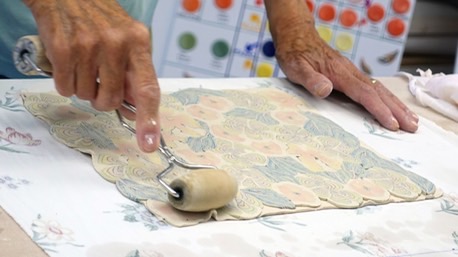
I let this piece rest on a damp towel beside a matching piece of plain white clay for at least one hour.
Then carefully place one on the other.
ROLL DOWN … do not stretch if you want the accurate pattern.
You can also roll it thinner at this point then let it rest for 15-20 minutes before making a piece.
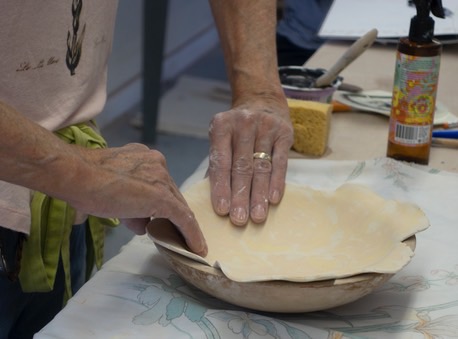
Shape and gently press into whatever form you are using.
Cover snugly with plastic and let it rest for one day without opening it. This lets the whole piece even out in humidity and helps prevent cracking.sdf
You can use sprigs without covering the whole sheet of clay.
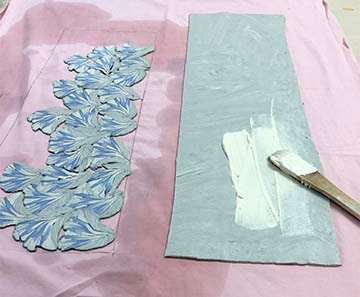
I covered the front side of this blue clay with white slip.
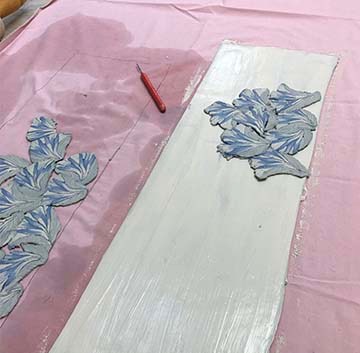
Then, I began to transfer the pattern to the slipped side.
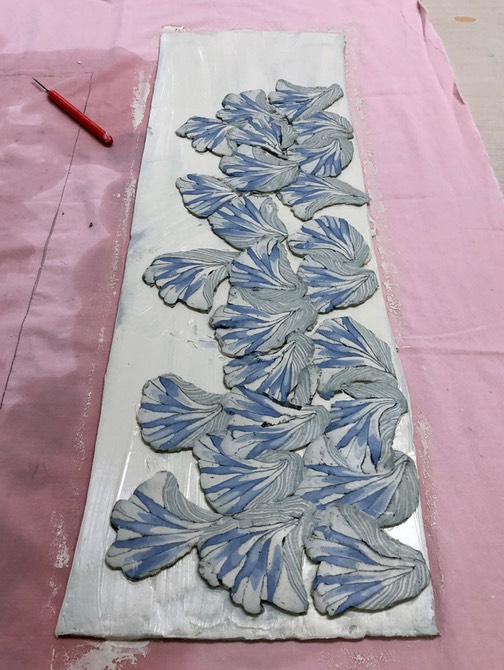
I patted them in place with care to press down, rather than stretching them.
When I was happy with the design I lightly rolled them to attach.
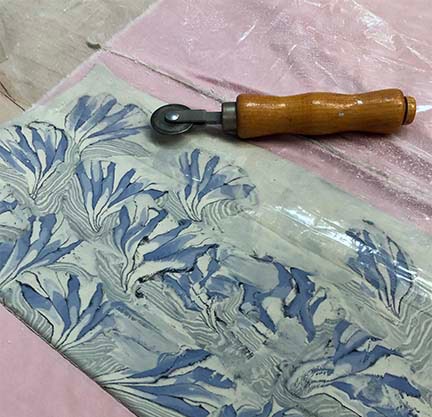

You could of course stretch them and move them any way you want for a wilder, looser effect.
Here is the vase made from this pattern.
SLAB ROLLER METHOD
This method was developed by Dean McRaine of Lightwave Pottery in Hawaii.
This is my take on his method, any errors are mine!
The basic idea is to get a large sheet of colored clay that looks a though it is only one piece of colored clay. This technique works best with a large, double roller, slab roller.
Start by preparing your plain piece of clay to the size you desire. Measure and mark both sides so you can easily place both colored sheets in matching spots.
Measure your colored sheets to be slightly narrower and shorter than the plain clay.
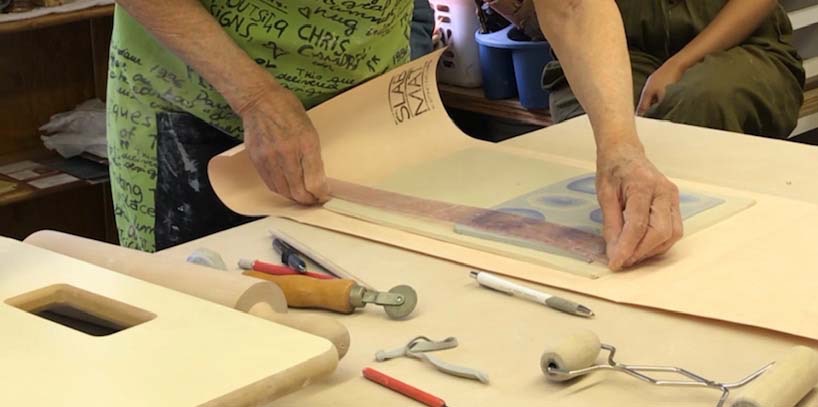
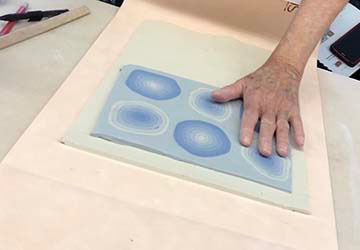
Place colored sheet about an inch from the top and leave a half inch on each side. A quick spritz of water or a thin coat of slip will hold it in place.
Flip the piece and place a matching colored sheet in the same place … the colored sheets are now matched up, back to back.
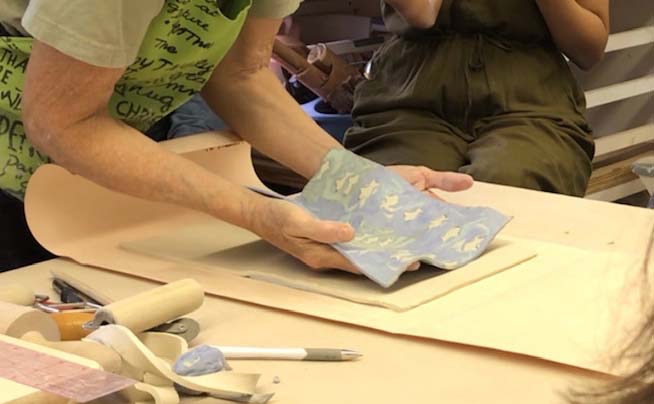
The trick is to pass them through the slab roller several times. With each pass, very slowly decrease the width … the slower you can do this, the less distortion your piece will have.
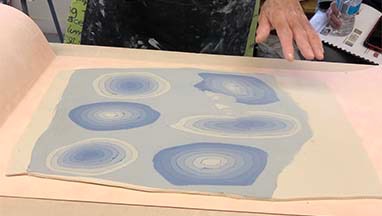
Some slab rollers are better than others at slowly reducing the opening for the clay. If you feel it grabbing you should stop right away or the whole slab will be distorted … which is not always bad news but is annoying if you didn’t want it to happen
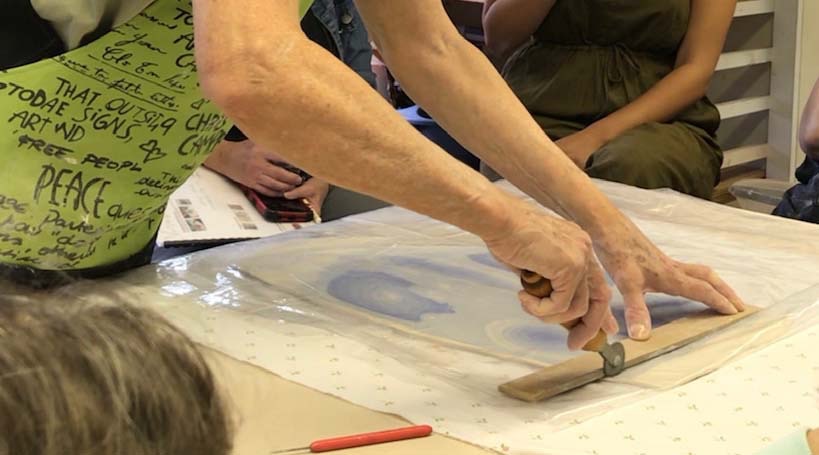
Now you can cut it to size with the spliner and use after resting.
THANKS to Dean McRaine for generously sharing this process, to Sue Weber & Barbara Zerbe for teaching me and to Erika Sanger and Judith Guberman for sharing their photos of my interpretation of his process.