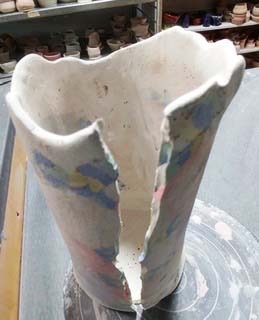
The number one ‘problem’ question I am asked is
“Why did this crack?”
Number 1 Tip
SLOW DOWN
Number 2 Tip
Control the Humidity
Your patterns and designs have thousands of places where the clay is meeting slip on a variety of angles. You have to give the clay a chance to rest and make sure each segment matches humidity wise before you move on to the next step.
When you turn it into a cane or a design … let it REST. Depending on the complexity and size it can require anything between hours to days for very large work. While it is resting the humidity is evening out, the slip is attaching to the clay, the whole design is coming together rather than staying in separate parts.
When you make a vessel SLOW DOWN. Make sure ALL pieces are at the same humidity. Cover the work with plastic any time you leave it to make sure it stays evenly humid. Give the work time to shrink back from any rolling process.
Once finished with the making, you cover the rims with paper, then cover the whole piece tightly with a double layer of dry cleaner type plastic then LEAVE IT ALONE for two days. Then you can open it and let it dry loosely covered with plastic, away from any drafts, sun or heat source.
If babying a piece goes against your nature, consider switching away from porcelain to a white clay body that is flexible and more forgiving. Something groggy that can stand a less fussy pace. You will sacrifice the translucent qualities of porcelain but this quality might not matter as much as ease of use does to you.
SO, what is the answer for the other cracks?
A sharp edged crack often means the kiln cooled too quickly.
Firing down your kiln will eliminate a large number of cracks that are caused by the rapid cooling of electric kilns. If you have a computer controlled kiln this is an easy fix … your owners manual likely has a controlled cooling program you can run.
SO, what is the answer warping?
Porcelain should be fired in its own support form since it cannot support itself when it widens out. Cylinders work fine and so do smaller bowls but once the form spreads out it needs support.
Sometimes it lies in design ... the shape of the vessel putting pressure on one point.
If all pieces are not the same thickness, warping can happen.
Large or badly balanced handles can cause warping by pulling the porcelain out of shape .
Everything goes slower with a thicker form … drying, heating and cooling. Rushing this can cause cracks as well as warping.
Sometimes, it is just a mystery that needs some trial and error to solve.